Projects Can’t Start Too Early
We’ve all been there before. The deadline is looming large and you’re sweating because the lead time on your furniture puts install at 2 weeks after the project “drop dead date.” Your client is breathing down your neck and the only answers you’ve got put the blame on them. Maybe it’s true, it’s their fault, but saying so isn’t a great career move.
It’s pretty common. Too common, in fact. New projects are always on a timeline that is unrealistic. Why? Because the “ideas” people rarely understand everything that goes into completing a buildout of some sort. Whether it’s new construction, renovation or additions, owners are pushing the delivery envelope[BO1] and are unlikely to have realistic expectations of the timeline.
So where’s that leave you? Luckily, we’ve got a halfway decent answer.
Before We Go Any Further – There Is No Silver Bullet
Let’s start with what this post is NOT. This is NOT a blanket invitation to give us a call when you’re 3 weeks out from an install deadline and expect us to meet your date. This is NOT a “get out of jail free” card. This is NOT a best-practice and should be understood as a LAST RESORT.
Can we be clearer? Did we leave something out? If we need to, we’ll leave a legal disclaimer at the bottom of this post. What we’re about to share with you is a tool that you can use IF you find yourself in a situation with no other options. DO NOT start planning your projects with this in mind.
All that being said, let’s get on with what this post IS.
Why Is Everything Always Late?
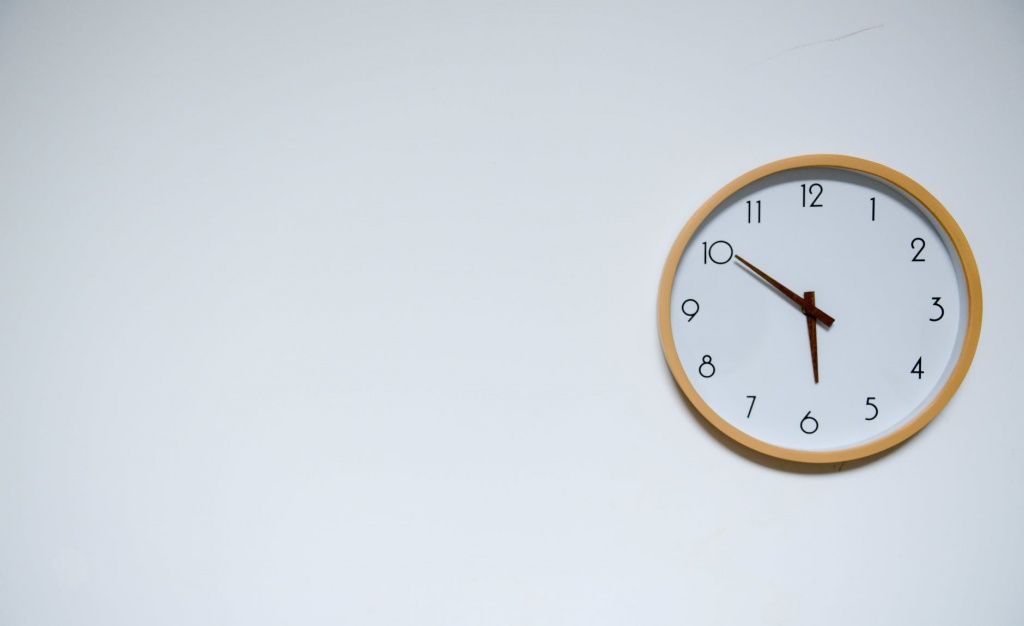
When an architect is designing something, their first priorities are usually functionality and aesthetic. What isn’t top of mind is that a particular material might be out of stock, or that “X” Molding takes 4 weeks longer to manufacture than “Y” Molding.
This shouldn’t be something you have to worry about, but it is. Project timelines are incredibly important and design has a significant impact on the amount of time the project takes.
When it comes to casework, there can be significant lead times involved. If the casework is not designed and ordered early enough in the project, it may not be possible to get it installed within the project timeline.
There are a number of specific reasons for the amount of time involved.
It takes a month for the manufacturer to make shop drawings
At the point that the manufacturer receives the PO, they need 30 days—or sometimes more depending on complexity– to return the shop drawings based on your designs. Every construction project requires shop drawings, so the sooner you can get the design to the casework contractor, the better.
Architects have to approve the shop-drawings
This isn’t always a problem, sometimes the architect approves the drawings quickly. It’s always a wild-card though, you never know if it’s going to take 2 days or 2 weeks to get the approval process.
Field measurements delay shop drawings
Field measurements are a must for casework because you need the fit to be as exact as possible. Oftentimes the completed structure in which the casework is being installed differs in measurement from the original plans. In order to make sure the shop drawings are accurate, field measurements need to be taken. This step can only be completed once the shop drawings have been returned and approved by the architect and the building is far enough along.
Cabinets have a 12 week lead time
Once the cabinets have been approved, it takes 12 weeks for the manufacturer to assemble them to the specifications. All cabinets are specifically cut and built to the specifications submitted from the field measurements and approved shop drawings.
Along this whole process, there’s plenty of room for things to go wrong as well. Factoring in 4 weeks for shop drawings, 1-2 weeks for architect approval and field measurements and 12 weeks for lead time, that’s 17-18 weeks. Also, those 17-18 weeks start from the point that the manufacturer has received the PO for the casework.
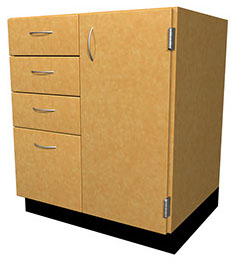
Casework In Real Life
February/March is when schools often begin planning for renovation projects that they want to be completed in August. From February to August is 6 months end-to-end. As we’ve just discussed, minimum planning time for casework is a little over 4 months.
By the time the project has reached the point where the manufacturer has been sent the PO, it could be June. Two months is not enough time to get the casework. In this scenario, there’s no way the casework will be manufactured in time to be installed before school starts again.
Where The Rubber Meets the Road
Up to this point, we’ve been discussing timeline challenges for a casework project that is based entirely on custom materials and finishes.
There is an option for architects when they find themselves against a wall and there appears to be no way out.
This option is not a catch-all, nor is it guaranteed to fix all of your timeline challenges. However, this could save your neck next time you have no idea how you’ll get casework installed within the project timeline you’re dealing with.
TMI Program
Earlier in this post we discussed the amount of time required to get casework manufactured when you’re working with custom cabinets following conventional manufacturing guidelines. We’ll call this the Traditional Order model.
Contrasted to the Traditional Order model, you can take advantage of what’s called “direct purchase.” We’re going to be specifically discussing TMI’s direct purchasing program.
The TMI Direct Purchase Quick Ship program is specifically intended as a quick ship option for projects that need casework delivery faster than the typical 12 week lead time. There is no sacrifice in quality or cost, but your options and project size may become more limited.
There are specific parameters required for the program. If these are not strictly adhered to, the project cannot fit into the Direct Purchase program.
Timeline Under Direct Purchase. Under the direct purchase model, you will design your cabinets based on what is available in the TMI Direct Purchase Catalog that consists of the top selling configurations.
You can read the TMI Direct Purchase Catalog here.
Instead of submitting a PO and waiting for shop drawings, an order is placed immediately. You receive confirmation of what was ordered, but no shop drawings.
At that point, you’re looking at 6 weeks until delivery of the finished casework, ready for install.
You’ll remember from earlier that the average timeline for traditionally ordered casework is 17-18 weeks. Using direct purchase, you’re getting your casework almost 3 times faster.
Frequently Asked Questions on the Direct Purchase Program
You can read a full list of TMI’s frequently asked questions here.
For quick reference, here are a few of the more relevant questions.
- When I make a laminate color selection what does this
cover?
- The laminate color selection will cover the cabinet faces (doors and drawers), both exterior sides of every cabinet ordered, and wall cabinet bottom panel exterior color.
- When I make a PVC color selection what does this cover?
- The PVC color selection will cover 3mm edge-banding on the cabinet faces (doors and drawers), and 1mm edge-banding on the cabinet body, including the bottom edge of wall unit side panels. The front edge of all shelves will be provided with white 1mm PVC to match the interior.
- I have some miscellaneous accessory pieces on my
project. How do I select their color?
- Miscellaneous accessory items which have color options (such as grommets, glass insert retaining strips, and countertop support brackets) will be provided in the color you have selected for hardware (gray, beige, white, and black). If chrome hardware is selected, these accessory items will be provided as black.
- After I send an order in, how will I know that TMI has
received the order?
- TMI will monitor the Direct Purchase orders throughout each working day. We’ll send you an order confirmation email which includes a project summary, components included in the order, color selections, and delivery information within one (1) working day. This will be your indication that the project has been input into our system and materials have been ordered!
- Are shop drawings provided by TMI?
- All the information TMI needs to produce the casework is collected online, eliminating the need for drawings. However, if you need to produce drawings to show your customers, download the CAD files provided on the project summary page. Each download contains the exact cabinet configuration and sizes you ordered so drawings will be simple for you to provide.
- Can I order locks and how will the keying be provided?
- You may indicate locks as required for each cabinet style by selecting the “lock” check box in the online programming. Disc tumbler, cam-style locks with removable cores will be provided. All locks for the entire job will be provided as keyed alike. There are no special locking requests available for this program.
Additional Resources
You can read the full TMI direct purchase specifications here.
You can read the full selection of direct purchase laminates here.
Keep In Mind
We want to iterate one more time, this direct purchase program is NOT a replacement for good planning. This direct purchase program is available to you if you find yourself in a position where you have no other option.