What’s a Fast Lab?
Private labs are a dynamic market. The demand for labs that can be flexible is rising rapidly, but so is the need to get your lab up and running immediately. In the private market, the real need is for labs that can handle a variety of potential testing applications and quickly adjust to changes in client needs.
This rising demand is creating a corresponding increase in the need for private labs to be flexible and quickly make changes to their environment. Sometimes a private lab ends up in the position where they have 2-4 weeks to get a lab environment built out or they won’t be ready for a client’s testing requirements.
This is what we call a “fast lab.” Fast labs are lab environments that need to be fully-functioning in 2-4 weeks. This is a common problem for labs in the private sector. In this post, we’re going to dive into the process you need to follow if you want to get a “fast lab” up and running.
Where Does It Hurt?
When you’re trying to get a lab setup quickly there are a number of considerations that you need to keep in mind. If you don’t stop for a minute and do a little planning, you will pay for it later.
The main thing you’re trying to avoid is getting it wrong the first time. Taking time to think through the project will help you avoid some of the potential pitfalls listed below.
- You waste money on something that doesn’t work for you. The last thing you want to do is get your lab up and running, only to realize that you can’t handle a major testing requirement. Not only have you lost money and time constructing something that doesn’t work, you’ve now likely lost the business you were constructing the lab for in the first place.
- The different components of your lab aren’t compatible. For example, you didn’t engineer the countertops right, so while the cabinets and lab benches are in place and ready to go, you’re now waiting 4 weeks to order new counter-tops. Now your process is starting a month late.
- You build it for now, but it’s useless in 12 months. This is the most likely scenario for the modern lab. The rate of change for testing requirements and client needs is increasing at a significant rate. If your lab environment can’t adapt, you may be saddled with serious inefficiencies, are become obsolete altogether.
So how do you avoid these issues? At the risk of sounding obvious, you plan. There are a few specific questions you need to ask yourself to make sure you’re getting off on the right foot.
Question #1: Do I understand all the implications of the testing requirements?
This is a common scenario. You build the lab, but it turns out that one of the testing requirements had a really specific specification need but you didn’t include it in the specs for the project. Make sure you are really clear on the materials, design, floor-space, etc…
Question #2: Is everyone involved in the project communicating with each other?
Just because you understand your vision, it doesn’t mean the contractors do. Sometimes this is the contractor’s miss, but it may have been your communication of ideas and expectations wasn’t good enough. To avoid re-doing things or delayed timelines, make sure everyone involved in the project is communicating and aware of the project goals and needs. Set regular meetings, keep a project log & shared documents repository, and this is a big one… track all changes!
Question #3: What’s next?
This is the most important question. Sure you may be building out a lab for a stellar new client. You may even have a contract with this client and are guaranteed 24 months of predictable revenue. What happens after this project is over? You’re spending all this money to build a lab environment, are you going to have to repeat this whole process 2 years? Or even 1 year?
Keeping an eye focused down the road is critical for making smart use of your time, money, and lab space. You want a flexible lab that can handle a variety of testing requirements and potential client needs.
How To Build a Fast Lab
If you really want to get your lab up and running in 2-4 weeks, you need to understand your options. Obviously, your selections are going to be limited because of the timeline you’re working with.
Sourcing
Sourcing cabinets, fume hoods and furniture is the biggest challenge you’re facing. Because of your short timeline, custom fabrication is out. This means you’ll have to plan to work within the parameters that are available from a pre-fabricated and stocked supplier.
In-Stock
There is an online cabinet and furniture source called instocklabs.com. These folks hold about 200 popular designs in stock, with a limited color pallet and set dimensions. Instock will allow you to get all the furniture and cabinet pieces you need within your 2-4 week time-frame.
Design
Because your options are limited, you will need to reference the Instock catalogue and plan your design accordingly. You can find the Instock catalogue HERE. There are usually a couple different stock dimensions available for the different furniture and cabinet pieces. You need to understand the dimensions of your room and design your layout based on the dimensions of the furniture and cabinets that are currently in stock. Focus on adjustable knee-space openings and fillers to complete wall to wall locations, and incorporate free-standing tables to work with fixes cabinet and sink elevations.
Layout
So you’ve got a clear plan and you’re ready to get started. Installation is the next hurdle you’ll be jumping.
Before you can install, you need to understand exactly how your cabinets and furniture are going to fit into the space. You also need to engineer your countertops to make sure they will fit correctly with the cabinets that you’ve ordered. Drawings are critical at this stage, and precise details and measurements will be crucial.
Here are the main points you need to be aware of when it comes to your space layout.
#1: Your sinks need to integrate into your cabinets. This means that your sink dimensions must fall within the dimensions of your sink below the countertop. Each cabinet will have a top flange that will reduce the clear space for the sink. If you have a 36″ wide sink, plan on using a minimum width of 33″. The same is true for the depth: pay attention to the front cabinet rail setback, and don’t forget the countertop overhang (usually 1″).
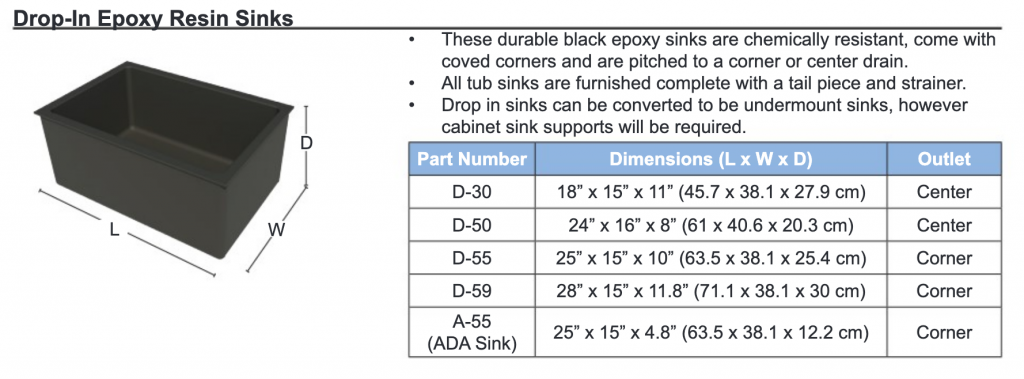
#2: Know how to space your fixtures. If you’re installing faucets, you’ll need to be aware of how much counter-top space you need to accommodate the number of faucet heads that you have. You also need to avoid any faucet-handle conflicts.
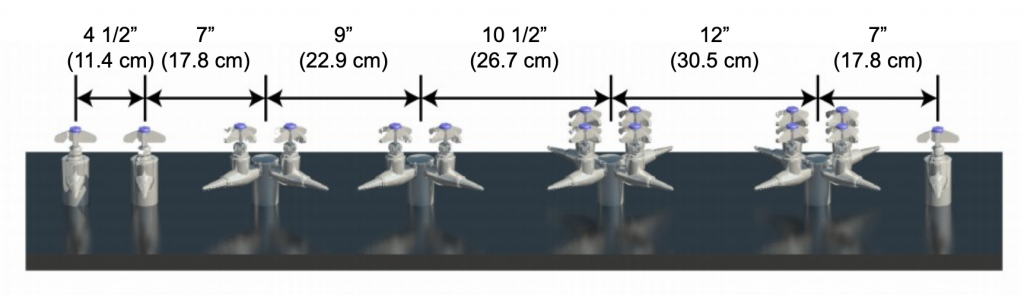
#3: You have to work with standard cabinet dimensions. Your options for pre-fab cabinet dimensions will be either 36″ or 48″ wide. This factors into all of your design and planning. You will also need to make sure that you get the right cabinet fillers to finish out the design because you won’t be able to perfectly fit the cabinets like you would if they were custom-built.
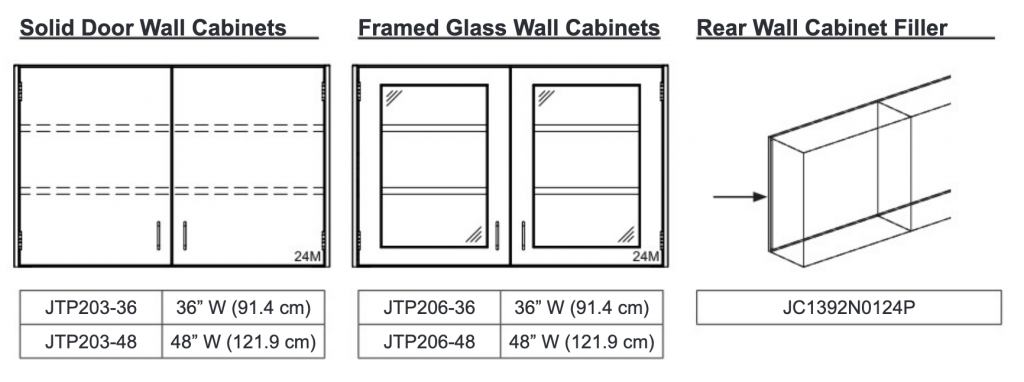
Installation
The cabinet installation shares similarities with general cabinetry, but make sure your installers are familiar with European style cabinets or steel cases (depending on your selection) and it is a must that they know how to join lab countertops properly.
Also, make sure you’re coordinating the trade process with your contractor so you get flooring, plumbing, electrical and other exhaust mechanics sequenced intentionally.
Flexibility
Up to this point, we’ve been discussing the basics of planning and installation. Now we’re going to look at things from a more strategic angle. Flexibility refers to the ease with which a lab space can be utilized for multiple applications. A flexible lab space is easily configurable for different personnel habits, testing requirements, and lab equipment setup.
Flexible lab spaces can be accomplished several different ways.
Rolling cabinets. Rolling cabinets are exactly what they sound like: furniture or cabinetry that has casters on the bottom so it can be easily moved around your space. Using rolling cabinets, like the ones below, will allow you to adapt to future lab requirements easily and cost-effectively.
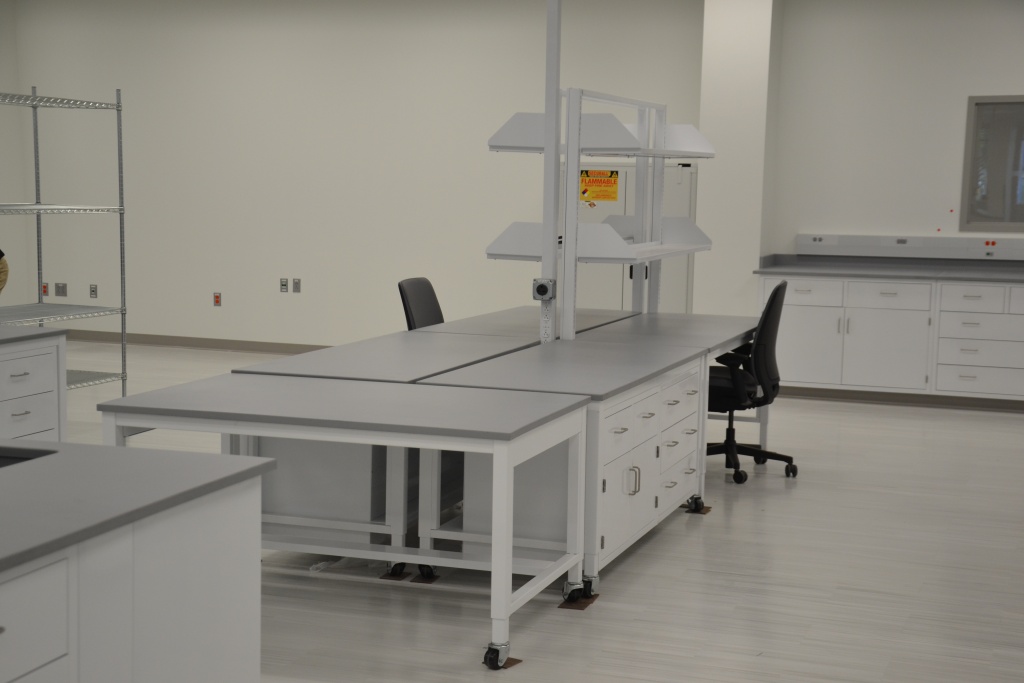
Adjustable shelving. Adjustable shelving is extremely important for utilizing counter-top space. Sometimes shelves need to be raised, or removed altogether, to accommodate a large piece of countertop equipment. Or perhaps the personnel height restrictions require lower shelving settings. Adjustable shelves bring significant flexibility to a lab space.
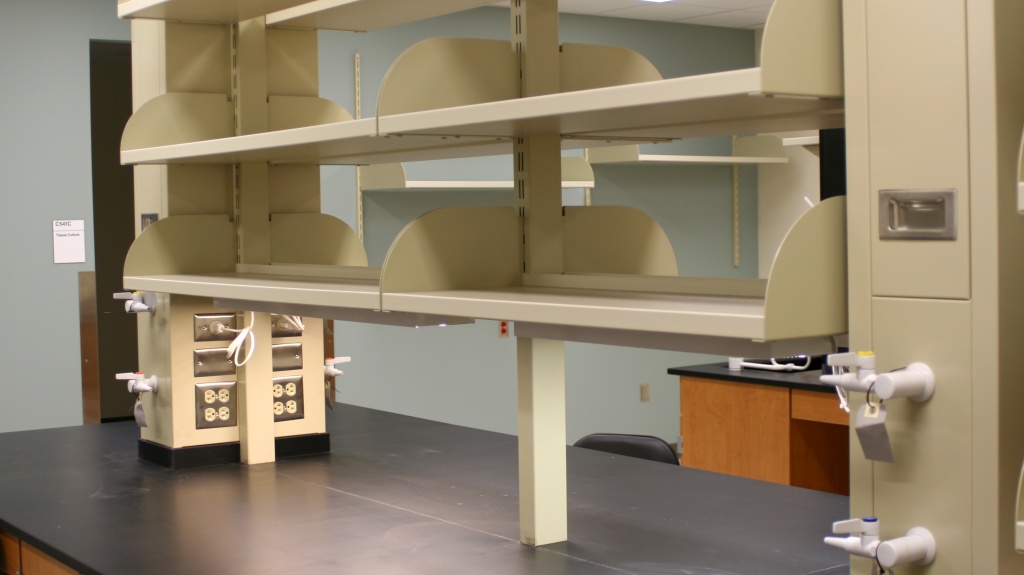
Adjustable Counter-Tops. Shelving isn’t the only consideration for adjustable furniture. The size of containers or measuring equipment can vary greatly. In these scenarios, being able to raise and lower the counter-top allows many different experiment setups to fit underneath services.

The counter-top underneath the faucet bank can be lowered all the way to floor if necessary
Health and Safety
Health and safety cannot be an afterthought in a lab setting. Health and safety implications Protecting lab personnel can include exhaust systems, electrical wiring and circuit protection, proper chemical storage, safety stations and even ergonomics.
- Fumes. Fumes are vapors, smoke or gasses from any kind of noxious or harmful chemicals. Any fumes that can either harm lab personnel or make the environment difficult to work in need to be ventilated somehow. Ventilation can be accomplish in 4 different ways.
- Chemical Fume hoods.
- Ventilated Enclosures.
- Local exhaust capture.
- Filtration systems
- Electrical Circuits. Electrical circuits are important because you need to make sure your furniture is rated correctly to handle the equipment needs of your laboratory requirements. You need to answer a few questions to make sure your equipment is prepared electrically.
- Are your electrical items UL listed?
- Are your electrical circuits ground-fault circuit interrupt protected?
- Do you have the right number of circuits in the furniture for the items that you need to power?
- User-Safety. User-safety includes ergonomics for personnel as well as height requirements and lifting safety. You’ll need to make sure that your lab environment can accommodate all shapes and sizes of workers as well as lifting capabilities.
- Repetitive injuries can be caused by workers spending too much time in poor positions. This includes counter-tops and workstations that may be too high or too low.
- Lifting injuries can be caused if a worker needs to lift a heavy piece of equipment or access tools on shelves that are too high or counter-tops that aren’t adjustable.
- You can run into efficiency issues if your seating is not adjustable because workers will need to get up and take breaks more often leading to less productivity over time.
Putting It All Together
Getting a lab up and running in 2-4 weeks is possible. It’s also a lot of work. It’s essential that you are planning ahead, taking stock of all the necessary requirements and keeping an eye on future uses for your space.
By following the guidelines outlined in this post, you can develop a highly-functional and flexible lab space within your short timeframe.