A history of lab workstations
Thomas A. Edison’s famous laboratories at Menlo Park and West Orange, New Jersey, are icons of the modern age of innovation and discovery. He boasted that his lab was the “best equipped & largest Laboratory extant, and the facilities incomparably superior to any other for rapid & cheap development of an invention, & working it up into commercial shape.”
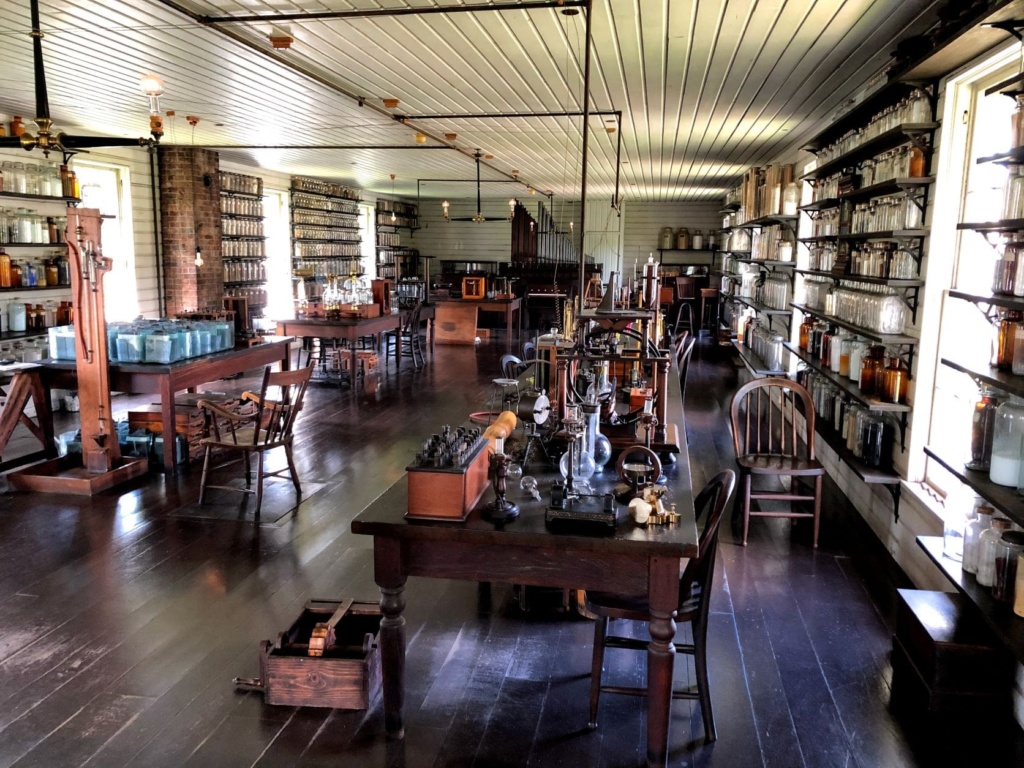
Edison set his sights on innovation and crafted his workspace to facilitate it. He kept all the tools necessary to speed his work close at hand, and designed the space for maximum impact. While the laboratory space itself was predominantly filled with large tables and shelves for supplies, it also had customized workstations with “unusual facilities” for perfecting inventions. These included a 10-horsepower engine and a rack of galvanic batteries. Some sections of the benches were lower for larger pieces of equipment. Some had different support or storage. Some were positioned over holes in the floor, to allow pullies and larger apparatus to reach from the first floor up to where the researcher would interact with the equipment.
When a laboratory is built, the goal is to create a space where work can be done, information can be gained, and processes can be managed. It is also important to develop the right work environment so that it becomes a catalyst to research, not a hindrance.
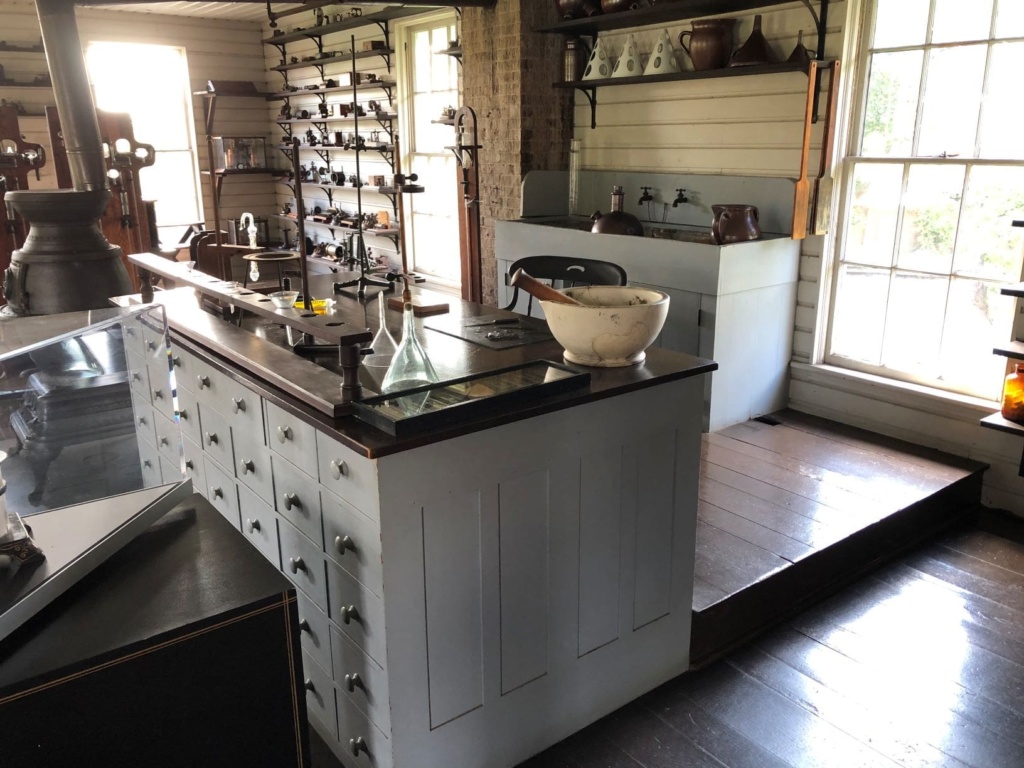
The simplest table might be all that you need for a researcher. Flat surfaces are best for most things that happen in a lab. But, everything that impedes work is a frustration and slows discovery. When something feels right, when things are in arms reach but aren’t in your way, it makes things work. Upon setting up shop in Menlo Park, Thomas Edison promised “a minor invention every ten days and a big thing every six months or so.” This is the kind of innovation and inspiration that can be fostered in the right laboratory environment.
In this guide we will be exploring the 6 most functional laboratory workstations and how they can be used in your lab space.
Fixed Research Benches
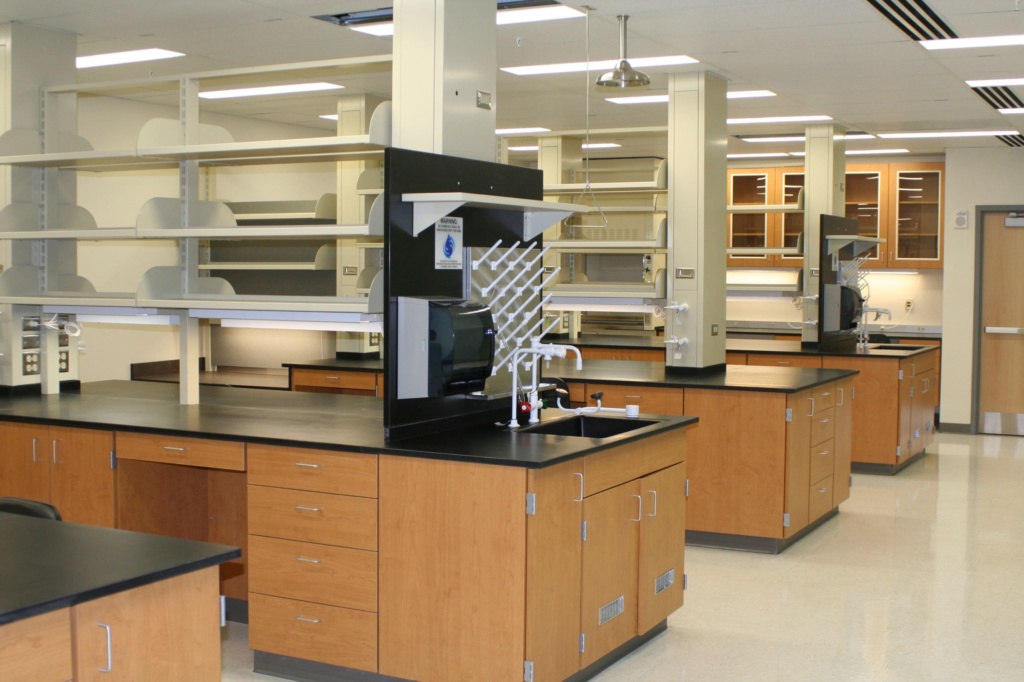
Fixed research benches are great for repetitive work, but they’re not flexible for new tasks. Structured layout islands and peninsulas are used in research laboratories because they offer a good value proposition. They offer the easiest way to deliver services for multiple research applications.
Fixed benches maximize storage by incorporating full-width undercounter cabinetry. This frees up workspace and increases storage capacity for the entire laboratory. An important feature of fixed research benches is their enclosed chase design creates an integral support system for electrical and mechanical services to be distributed along the bench.
More than this, they provide a consistent design and layout that is easily repeatable and does not encourage favoritism amongst research staff. To further increase flexibility, fixed research benches can incorporate adjustable overhead shelving. This allows for the most adaptable incorporation of different storage elements.
The stability of this system is beneficial for fine calibration instruments and precision instruments susceptible to vibration. They also offer the largest continuous, uninterrupted worksurface.
There are attributes of fixed research benches that do not fit with every application. For instance, they cannot be adapted without a construction crew, incurring significant cost and disruption. In addition, damage to one unit in a run can be difficult to address without disrupting the entire bench. Rigid aisle spacing can be limiting as staff load fluctuates (back-to-back researchers). Finally, fixed research benches to not adapt for large, full sized equipment like freezers, incubators and process stations.
Ideal Uses:
- Institutional research settings.
- Environments needing uniform architectural/lab planning efficiency.
- Education settings, especially ones involving student equipment storage or other lockable requirements.
- Lab spaces that require easy distribution of mechanical and electrical services. The incorporated chase can manage plumbing, waste lines and supply, as well as electrical and data neatly ordered under the work surface.
Flexible Table Systems
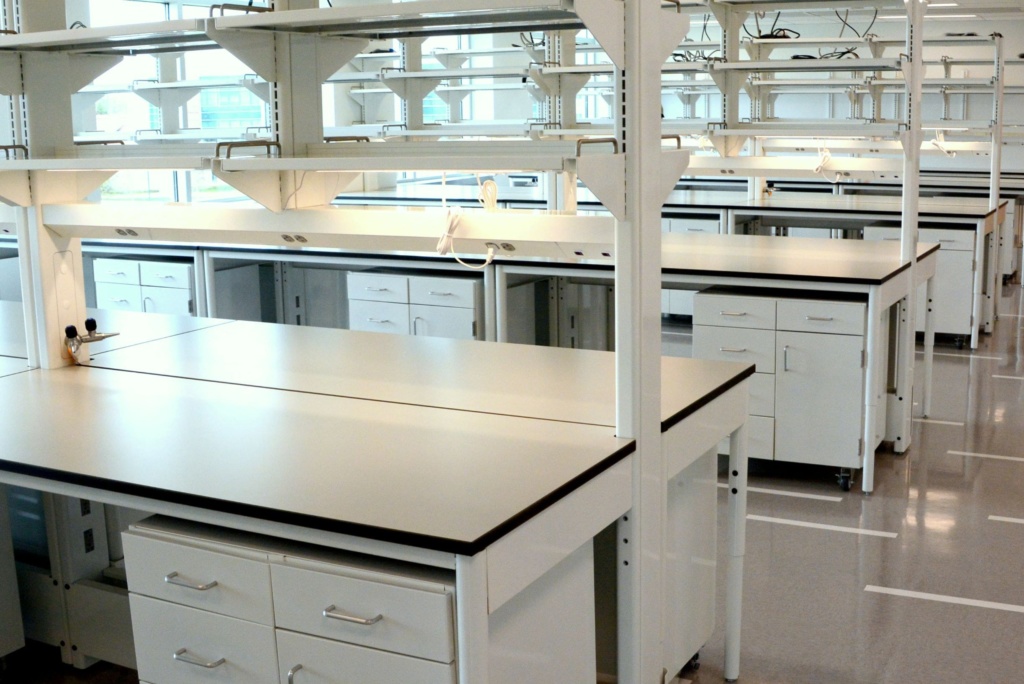
Flexible table systems are a hybrid between a fixed research table and mobile table. They offer the stability, storage and service access of a fixed research bench but allow quick reconfiguration without major reconstruction. These are not permanently fixed to the building, so they can be easily relocated to accommodate different lab layouts or changing equipment requirements. A work surface and shelving can be removed to accommodate an incubator and freezer without disrupting electrical or mechanical services.
The concept of these “tabling” solutions is that a leg or frame system transfers the load of the worksurface and overhead shelving directly to the floor. This design delivers greater weight capacity for equipment and experiments without having to attach these units to the building structure for stability.
This means benches can easily be adjusted in height or moved around by a building maintenance team without involving a contractor. Thus, they can also be quickly adapted to different situations which present in the laboratory.
Flexible table system worksurface heights can be adjusted for different processes or user accommodations. Sections can be removed to accommodate new pieces of equipment or testing carts without disrupting adjacent units. These table systems are quickly adaptable for ADA accommodation and can incorporate the same type of overhead shelving common in lab environments.
These are not permanently fixed to the building, so they can be easily relocated to accommodate different lab layouts or changing equipment requirements. A work surface and/or shelving can be removed to accommodate an incubator, freezer or new analyzer without disrupting electrical or mechanical services.
Depending on the manufacturer and design, flexible table systems may be wobbly and allow too much movement or they may be unable to handle larger pieces of equipment. As a baseline requirement make sure equipment complies with SEFA-8 and has been independently tested, but also take stock of what processes will occur in the lab and design accordingly. As an example, processes susceptible to vibration for calibrated instruments or weighing applications would be better accomplished on fixed benches (perhaps at the perimeter of the lab) or task specific specialty benches.
Storage is diminished compared to a fixed solution and typically involves mobile cabinets. This design feature trades maximized storage for great flexibility and adaptive applications. Since the cabinets are not themselves part of the support system, the leg framing takes up space at each unit which could otherwise be used for storage. Mobile cabinets are more expensive than fixed, but that increased unit cost can be offset because a lab might not supply as many at the initial commissioning. Your storage needs and adaptation requirements will determine what solution is best.
The engineering specifications of these benches are essential and warrant independent lab certification. You need to be sure that loads and anti-tipping calculations are validated. Benches have to be independently UL listed since electrical systems are embedded, but beware this hampers design customization, so expect to stick with cataloged items.
Ideal Uses:
- Research labs with processes that may change frequently.
- Incubator lab spaces. These stations can adapt to new processes, different equipment needs and flexing staff requirements.
- Private research facilities that may benefit from tax advantages due to classification of the lab casework as furniture.
- Spec-built tenant facilities where furnishings can be kept in stock for rapid deployment.
Height-Adjustable Workstations
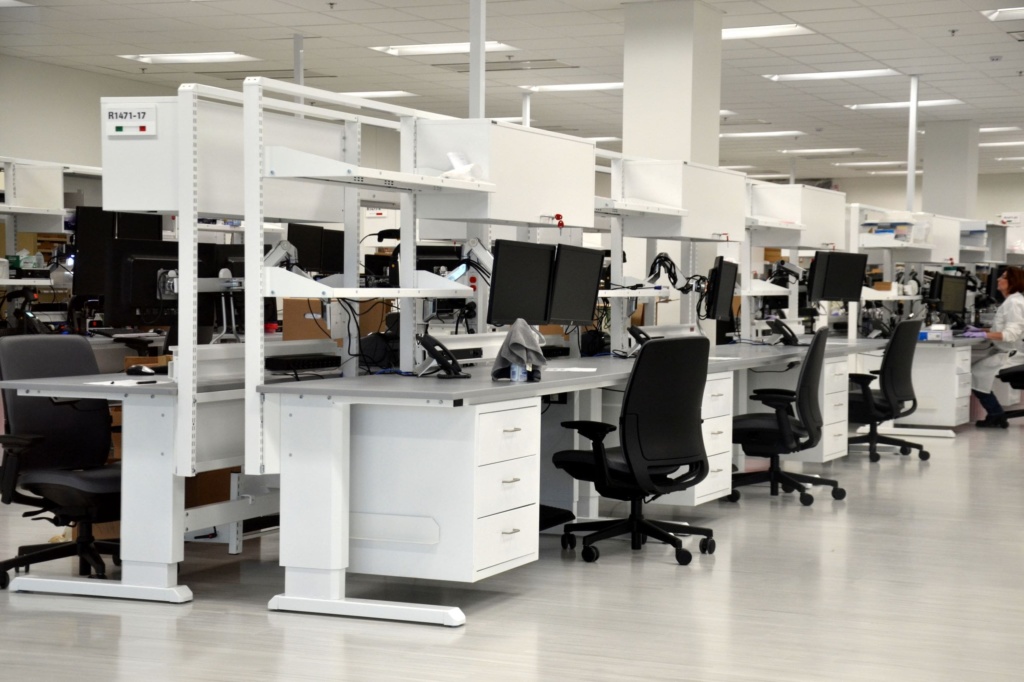
Height adjustable workstations are best explained using an example. We worked with a global medical device provider that wanted height-adjustable systems so their people could sit or stand. We selected the workstations pictured above and customized them to meet the needs of their FDA-compliant processes. This was part of a global workforce initiative to keep employees active and moving throughout the day.
These workstations also allowed them to adjust the work surface height so it was comfortable for charting and computer documentation but could be adjusted to “dock” with mobile equipment carts. These individual benches give the user maximum customization and flexibility to adapt on-the-fly.
Height adjustable workstations can be motorized tables which move at the push of a button. Other options include hand-crank and manual-height reconfiguration. User groups that have multiple individuals using a workstation, serve personnel on different shifts, or even dedicated users who value mobility and adaptability have adopted this solution in their laboratories.
The ability to make adjustments to the workstation height keeps laboratories from having to penalize or encumber users that would not be comfortable at a rigid or fixed-height station.
The ADA requires employers to provide accommodation to enable people with varying physical limitations to engage in the workplace. Using an electrically height-adjustable workstation is perhaps the best method to ensure intelligent compliance.
Whether your staff are wheelchair bound or taller than average, you can make sure they are accommodated no matter what their ergonomic requirements.
Ideal Uses:
- Environments needing to adapt readily to different user requirements.
- Labs that need to address ADA requirements. Height-adjustable work surfaces can change from standing to ADA or sitting levels with simple tools or automatically.
- Spaces designed for the health and safety of users. [ Callout box: includes this information]
- Labs with multi-shift or multi-user workbenches.
- Environments needing the widest selection of accessories and productivity-enhancing configurations.
Equipment Carts
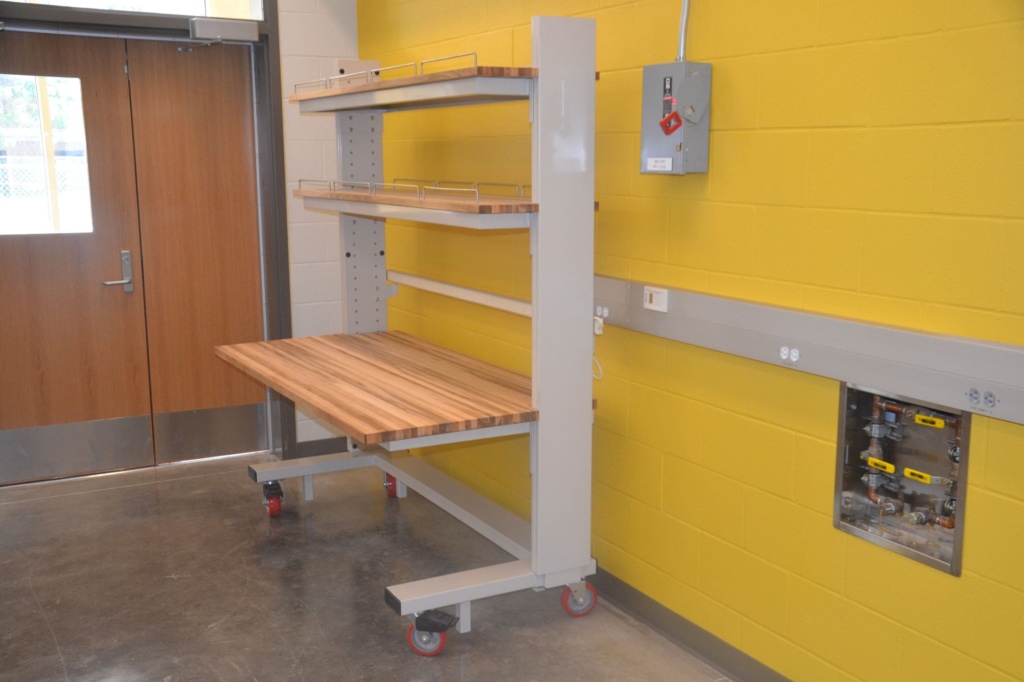
An energy production and conservation test laboratory at a major engineering university needed high-capacity equipment carts that could handle particularly heavy dynamometers and sensitive measurement equipment.
These carts (pictured above) were an ideal solution. They had the weight capacity to manage the equipment but also had adjustable overhead shelves to wire-in the computers and monitoring equipment.
From this point, the entire cart could be rolled where needed: station to station, and between laboratories to maximize the investment that had been made into the equipment. These heavy-duty and relocatable carts allow researchers to share high-cost equipment or setup complex testing equipment that can be used in multiple locations.
Equipment carts are engineered to be stable regardless of the equipment load placed on them. They are designed and tested to be mobile and incorporate anti-tipping features. In addition, they are intended to accommodate suspended cabinetry to maximize storage and user functionality.
Ideal Uses:
- Teaching and research laboratories.
- Labs needing to share high-dollar resources within laboratory groups for efficient use of constrained resources.
- Environments with unpredictable or not ideal flooring conditions. Isolating feet can keep surfaces level and limit vibration for sensitive equipment.
Mobile Tables
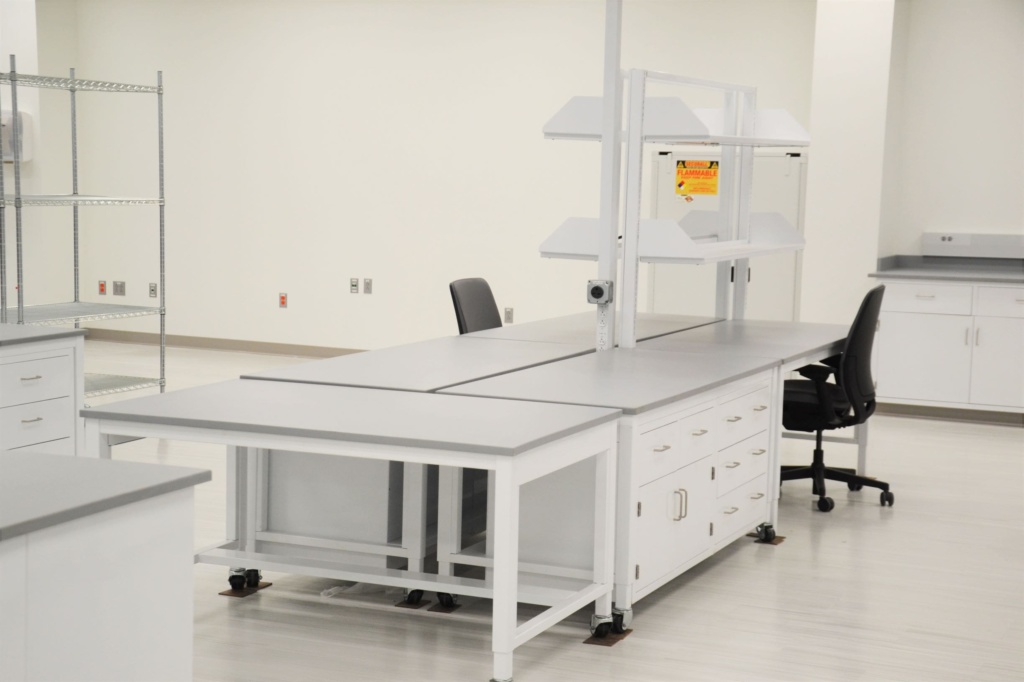
The ultimate in flexibility, mobile tables allow lab users to accommodate new processes and systems immediately. Plus, they have new options for service distribution. Often we see mobile tables used to compliment other types of bench configurations.
For instance, 80% of a laboratory may have a traditional, fixed-bench design, but every other station could have a mobile table docking to that system. This design strategy solves a couple of problems. It gives a user flexibility to raise and lower a section of their bench readily to handle unique processes or equipment. It also allows a table or a section of the bench to be removed if large, floor-mounted equipment is needed with a new process.
It can be common that when a space is designed by an architect or a lab planner, they do not know what operations or researchers will ultimately fill the space. To provide a measure of flexibility, mobile tables are incorporated in the design phase. These can be adapted with no need for outside contractors or facilities staff.
One of the key factors is that the mobile tables be engineered to seamlessly integrate or mate with the other bench systems. It would significantly disrupt processes if the mobile table’s surface were a half-inch higher or lower than your fixed workstations. These Incorporate locking casters for stability and can also include optional, isolating casters that level to uneven floor surfaces and create vibration isolation.
Whether you have some things on leveler feet or fixed-height cabinets, the tables should fit next to them without creating a barrier or hindrance for the researcher.
Ideal Uses:
- Lab spaces with ever-changing processes benefit from caster-based systems which allow users to adapt the environment as-needed.
- Environments with equipment sharing needs. Equipment can be placed on one table and moved station-to-station to save on capital investment costs.
- Spaces where fixed workstations sometimes need to be augmented. Mobile tables integrate or “docks” with other fixed or adaptable workstations.
Process Stations
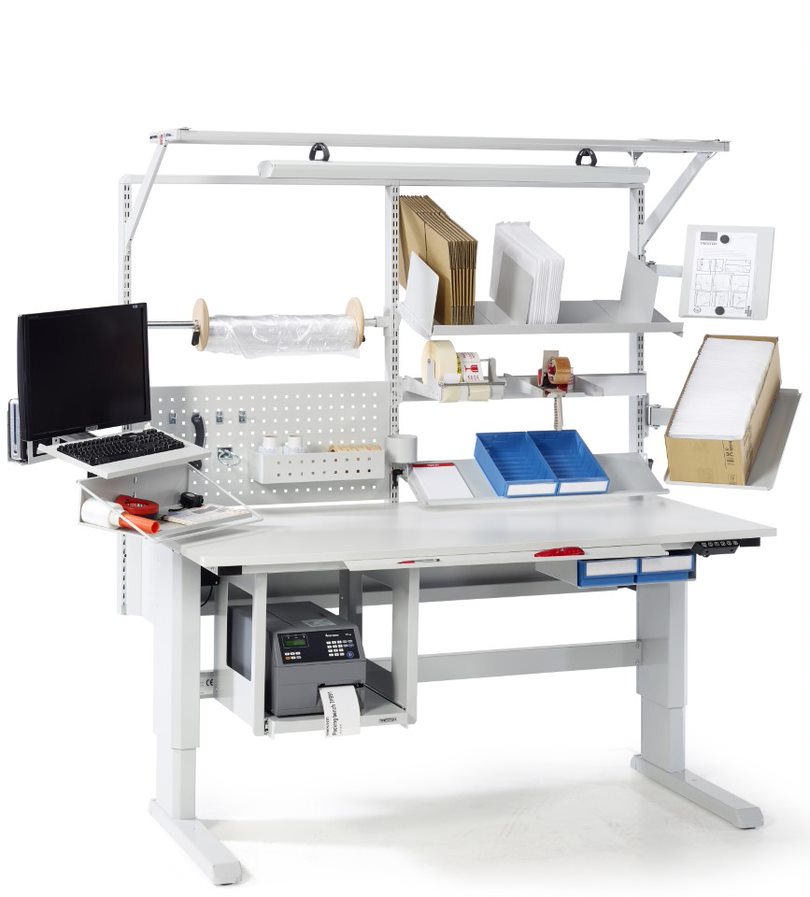
Process stations are designed for users with varied or complex needs to complete their work. As you can see in the image above, process stations are especially good for keeping a variety of tools and supplies within easy reach of the user.
Process stations can include things like customized cabinets with a special draw that can be pulled out to maximize space and flexibility in the cabinet space. These can be accommodated to a height-adjustable bench, or a fixed-height workstation.
If you need to increase the efficiency of a normal lab workstation space, process stations are a good way to do it. They lend themselves to repetitive tasks and can reduce strain on employees by optimizing reach length and work surface height and sight-lines.
Customized overhead and user-interface support benches are developed with individual processes in mind for maximum ergonomic and efficiency advantages.
Process stations provide efficient, effective ways to perform tasks that would require three times the amount of space on an ordinary workbench.
Ideal Uses:
- Processes that involve repetitive tasks. It’s worth the investment to customize a workstation that puts everything within reach.
- Kit pack assemblies for bio-pharma. Any applications that involve packaging test or trial or lab sample gathering, such as COVID-19 testing, where you need access to multiple test-tubes, vials, instructions, and barcoding, plus packaging supplies.
- Electronics assembly and testing. Precision work with multiple components and testing equipment for repetitive tasks.
- Multi-shift work where different users need customized ergonomics.
- Quality assurance systems involving multiple ways to check equipment for malfunctions.
Picking The Right Workstations
Modern laboratories tend to integrate more than one type of workstation. Talk to your local support rep for more ideas on how to select the best workstations to suit your needs.